1000 glazed roof sheet roll forming machine parameters
1 | Main motor | Brand: Siemens Motor power: 4kW/5.5KW/7.5KW or as actual demands |
2 | Hydraulic power station | Brand: Shanghai Lichao Motor power: 3KW/4KW.5.5KW or as actual demands |
3 | Hydraulic pressure | 10-12MPa according to the oil pump and pump motor |
4 | Voltage | 380V/ 3 phase / 50 Hz (or as your requirements) |
5 | Control system | Automatic PLC control system (PLC brand is Siemens) |
6 | Mainframe | 350mm H beams / 400H beams according to machine demands, from China Tangshan Iron and Steel/ China Hebei Iron and Steel |
7 | Wall sheet thickness | 16mm/18mm/20mm/22mm according to machine demands |
8 | Chain size | 1 inch/1.2inch according to machine demands |
9 | Feeding material | Galvanized steel coil/color steel coil/aluminum steel coil |
10 | Feeding thickness | 0.3-0.8 mm |
11 | Productivity | 0 - 25m/min (according to machine specification) |
12 | Roll station | Common 11rolls or 25rolls (according to different design) From Baosteel, Tangshan Iron and Steel, Jinan Iron and Steel |
13 | Roller diameter | 70mm / 75mm / 80mm (depends on different design) |
14 | Roller material | 45# steel |
15 | Cutter material | Cr12MOV, from China Shanghai Baosteel or Japan Xiangpu Steel |
16 | Cr-plating size | 0.05 mm |
Roof sheet roll forming machine production process
Drawing confirmation
——After confirming the final profile with the customer, the team of 12 engineers worked out detail workable parts CAD drawings;
——After 5 recheck, the production manager arrangement the material for all machine parts;
Start production
——Our company owns 12sets rough lathe machine, 20sets precise lathe machine, and 30sets shearing machine, all machine parts start to manufacture.
Product Inspection
——Our company Own 3sets hard test machine, and 4sets surface thickness Chromium test machine.
——Roller and shaft: Our Inspect team test 90% wheels and shafts, confirm all parts size precise and performance after processing.
——Our Inspect team test all roller surface, confirm all part surface paint above 5um.
——Mainframe and medium plate: Our Inspect team tests the mainframe and plate cutting precise.
Assembling machine
——5 workers assemble and welding one machine body frame by three days.
Machine painting
——putty ensure weld parts surface smoothly, and environment-friendly paint ensures protect worker body and environment.
Machine Manual use test
——Confirm the output sheet tolerance within 2mm.
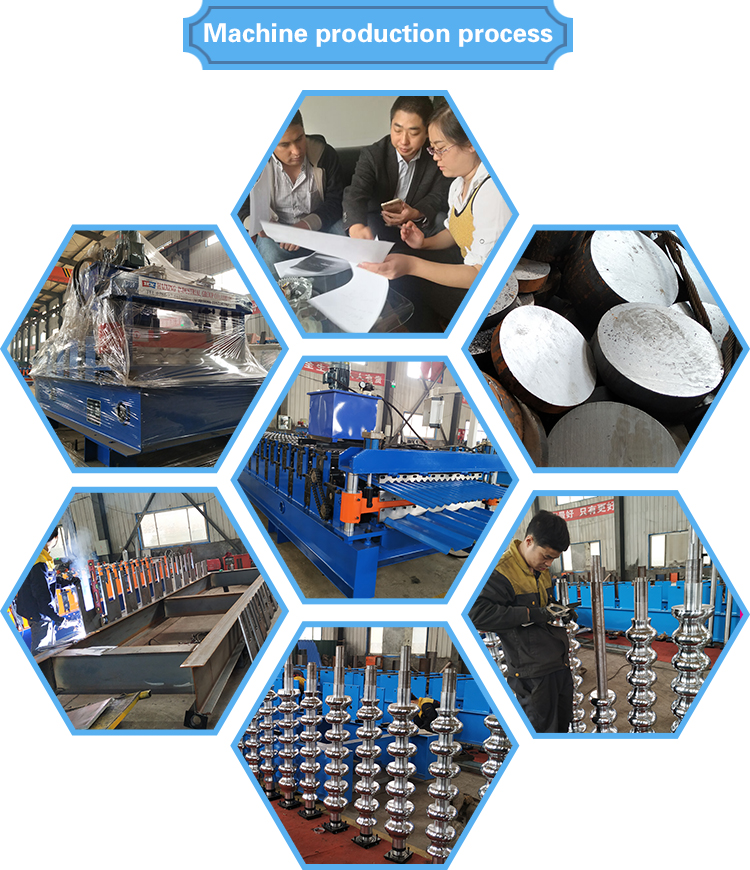
Cutter production
——According to the finally manufacture sheet, confirm the blade precise profile, Cr12MOV steel cutting knife finished by laser cutting.
Storage
——To protect the machine surface clear and without damage, we paint again and package by the film.
CONTACT US
E-mail: info@haixingsteel.com Phone/Whatsapp: +8615522419684